鉄筋コンクリートで構造物を作る際に、避けて通れないもののひとつが配筋検査です。コンクリートの芯として配置される鉄筋のサイズや数量、種類、鉄筋同士の間隔などが、設計図面(配筋図)どおりになっているかをチェックするもので、地震国である日本においては、構造物の品質や耐久性を担保するための重要なプロセスながら、多大な手間と時間を要する現場泣かせの仕事でもありました。ところが、この検査を大幅に効率化する画期的なソリューションが実現したということで、開発に携わった3人に話をお聞きました。
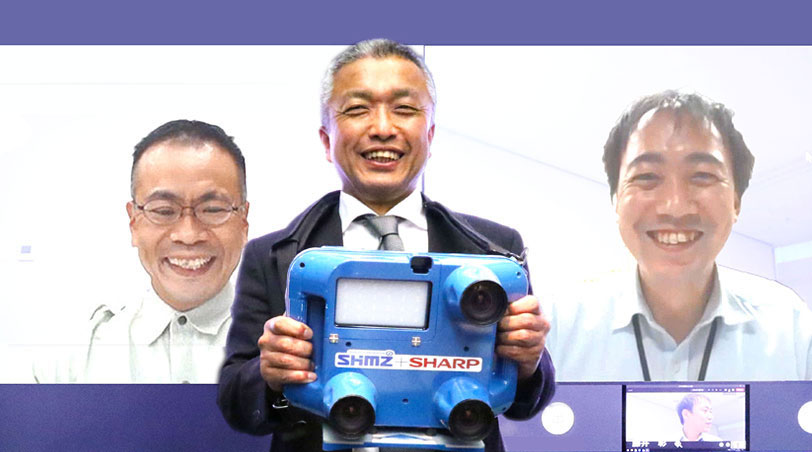
現場泣かせの配筋検査を効率化
これまでの配筋検査は、検査用具の準備、現場でのマーカーや検尺ロッドの設置、計測とその結果の記録、報告・提出のための帳票作成など、実に多くの作業が必要となる仕事でした。発注者による配筋の出来形確認では施工者3名、発注者監督員1名での作業となるのが標準的で、当然ながら、構造物が大きくなればなるほど検査対象は増え、作業員の負荷も拡大します。これを大幅に効率化することができるのが「3眼カメラ配筋検査システム」です。
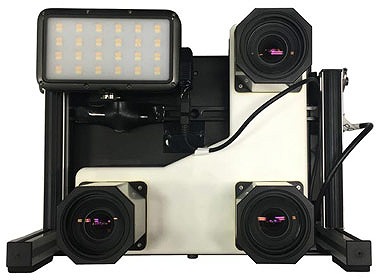
その外観はタブレットPCに3つのレンズが配置されたカメラユニットをセットしたようなユニークなもの。この3つのレンズは右下部のレンズを基軸に、右上部のカメラが垂直方向、左下部のレンズが水平方向と、2つのステレオカメラを組み合わせた構造になっており、撮影した画像はレンズごとに微妙にズレが発生します。このズレから三角測量の原理を応用することで、鉄筋の3次元位置を測定し、ターゲットの鉄筋の輪郭や位置を特定します。すると鉄筋の径やピッチ、本数などが算出され、自動で帳票を作成します。要する時間はわずか7秒。つまり、測定すべき範囲の配筋を撮影するだけで、あとはシステムが自動的に検査結果をとりまとめてくれるスグレモノなのです。開発プロジェクトを主導した吉武はその動機を次のように話します。
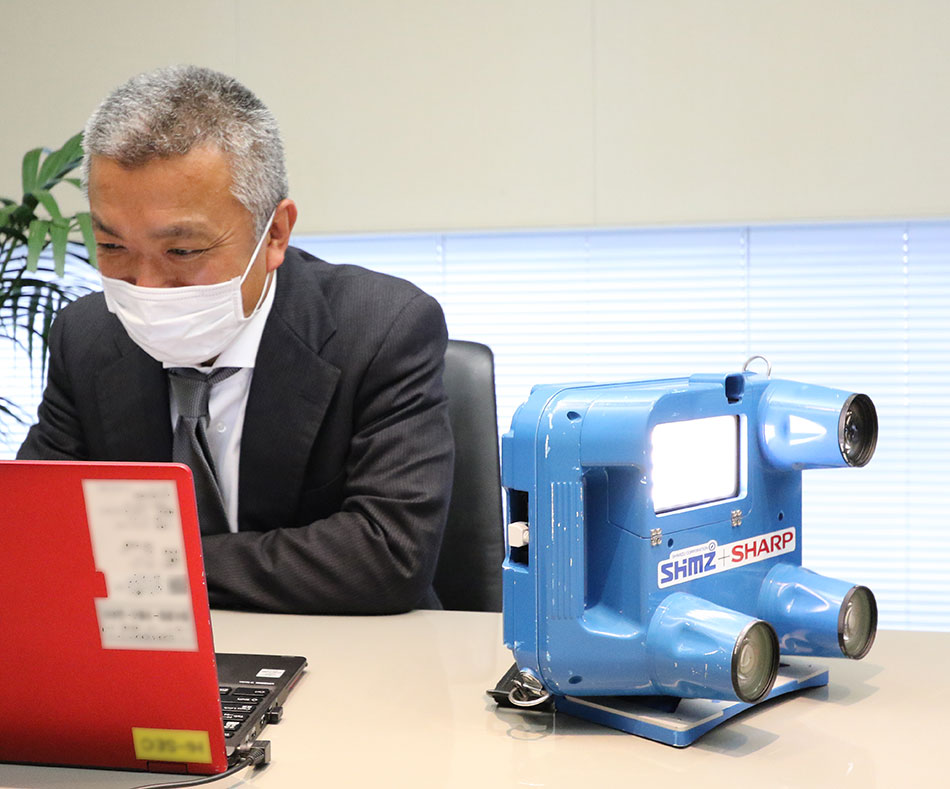
「配筋検査は非常に手数と時間がかかる工程です。なにより私自身が配筋検査が大嫌いで(笑)。この手の面倒で大変な作業は、入社3年目迄くらいの若い人に押し付けられがちです。でも次代を担う人材には、もっと別のことに取り組む時間を作ってあげたいという思いがありました」(吉武)
そう話す吉武は、これまでも鉄筋コンクリートに関するさまざまな技術を開発してきたエンジニア。以前、紹介した3Dプリントによるコンクリート積層技術「ラクツム」の開発にも関与する、鉄筋コンクリートのスペシャリストです。
開発当初は2眼だった?
共同開発者としてこのプロジェクトに関与したシャープ株式会社の有田氏は、開発の経緯を次のように振り返ります。
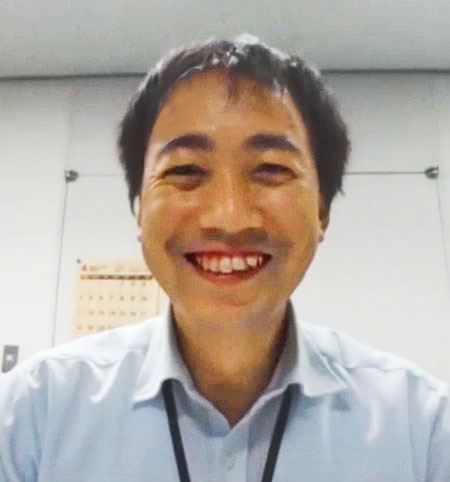
「清水建設とシャープでは定期的に技術交流会を実施しています。あるとき、ステレオカメラを紹介した際に『配筋を測れないか?』と尋ねられまして。当時は配筋はもちろん、鉄筋のことも何もわからない状態でした」(有田氏)
有田氏は吉武らとの対話を重ね、実際に現場に足を運びながら、鉄筋のサイズ感、現場ではどう配置されるか、現場の条件、効率を最大化できる検査方法など、開発に必要なポイントをひとつひとつ確認していったそうです。
「開発当初は、一日ぼーっと鉄筋を眺めながら、どう検出すればいいのかと考えたり。本当に手探りからのスタートでしたね」と有田氏は笑います。
「有田さんにはご苦労をおかけしましたが、この技術は撮影した画像内でターゲットの鉄筋を特定する解析技術がキモ。有田さんのようなプロフェッショナルの画像解析ノウハウと、私の鉄筋に関する知見と全国の現場で活躍する仲間の知見を組み合わせれば、より早く開発できると判断しました」(吉武)
2018年5月に最初の打ち合わせが実施された後、12月にはプロジェクトとして始動。2019年1月頃には最初のプロトタイプが完成します。当時はカメラ本体も大きくレンズはふたつの2眼、ストロボも別建てになっていました。
「取り回しやコストの点から2眼にしたかったのですが、より高い精度を得るためには3眼が最適とわかりました」(吉武)
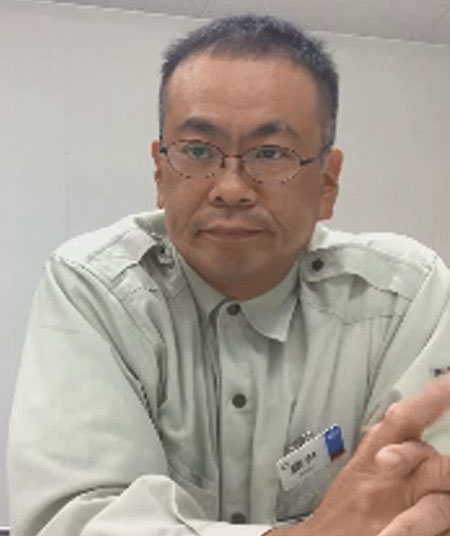
こうした現場の課題解決ソリューションの開発には、現場での検証が不可欠。ここで尽力したのが東北支店の藤井でした。
「新しい技術を試したいという技術者の気持ちはよくわかります。しかし現場としては工期を遅らせないのが至上命題。新しい技術は現場作業者の負荷を増やすことにつながりかねないので、敬遠したいのが本音です。ところが3眼カメラシステムはかなり仕上がった状態で話を持ちかけられましたし、実は私自身がチャレンジが好きなタチで(笑)。快く協力させていただきました」(藤井)
藤井らの意見を取り入れ、撮影画像に対する電子的な計測尺(電子ロッド)を実装するなど、3眼カメラシステムは少しずつ、しかし確実に完成度を上げていきました。
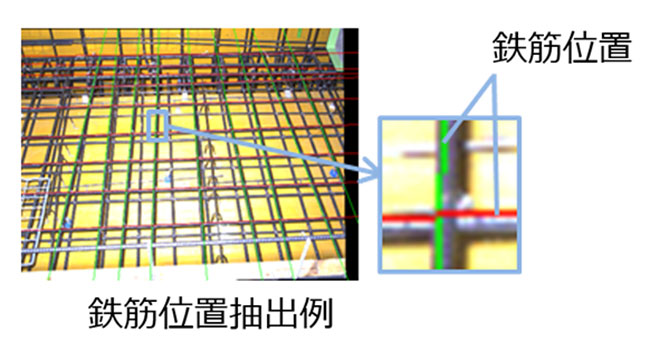
インフラ分野DXのキーソリューションとして
システムとしての完成度が高まる一方、吉武はこの技術の対外的な評価を高めることにも積極的に取り組んでいました。そのひとつが内閣府の官民研究開発投資拡大プログラム(PRISM)の資金を活用した国土交通省の「建設現場の生産性を飛躍的に向上するための革新的技術の導入・活用に関するプロジェクト」への応募です。国土交通省発注による東北中央自動車道の東根川橋上部工工事において、配筋検査手法として提案し、デジタル配筋検査システムとして本邦初の採用に至りました。
さらにハイライトとなったのが、2020年7月、国土交通省のインフラ分野のDX推進本部立ち上げの際に、DX技術の具体例として選定され、国土交通大臣にデモを実施したこと。和歌山県・二色トンネルの現場での配筋検査と、発注者による遠隔臨場の様子を、約435km離れた国土交通省の大臣執務室にリアルタイムで届けることに成功したのです。
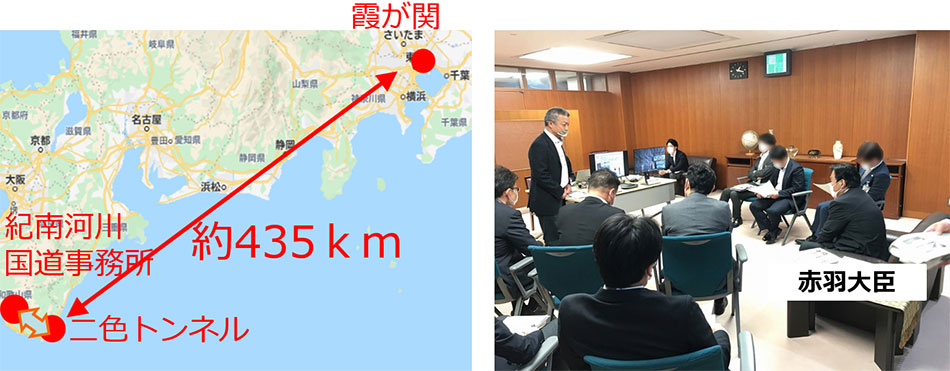
「冗談半分でしょうが、デモに失敗したらクビだと脅されまして(笑)。準備期間はわずか2週間。どのようなシナリオ、どこの現場で実施するのかなど、バタバタで準備を進め、なんとか成功させました」(吉武)
現状の3眼カメラ配筋検査システムのパフォーマンスは、上記した東根川橋での例では、3名・20時間を要していた配筋検査を、1名・5時間で完了しました。現場作業時間に換算すれば実に85%削減。非接触・少人数での検査により新型コロナ感染症対策にも有効。検査結果は撮影画像と紐付いたデジタルデータで保存されるため改ざん不可能で遠隔臨場とも親和性が高いなど、いいことづくめのソリューションに仕上がっています。
「でも、もっと軽くできるでしょうし、性能的にも機能的にも改善ポイントはたくさんあります」という有田氏に応え、藤井も「いろいろな現場で使えば使うほど、改善点や欲しい機能も出てくるでしょう。今後も協力は惜しみません」と意気込みます。
最後に吉武は次のように締めくくりました。
「配筋検査ソリューションの決定版となるように開発を進め、いいところまできたと思います。配筋だけでなく構造物の出来形確認をはじめ、高精度な寸法計測が必要なシーンへの展開も考えられるでしょう。こうした技術で現場のDXが進めば、3Kを脱却して若い人が希望を持てる建設業界に変われるはず。目指す本当のゴールはそこです」