当社は、3次元曲面で構成するデザイン性の高いガラスファサードを高精度に構築できる「3次元曲面ガラススクリーン構法」を開発しました。
本構法は、複雑な形状の曲面ガラス部材を点支持構法により接着接合するものです。支持部材を3D金属プリンタで一品生産することで構造的に最適化し、施工の効率性や品質の確保を実現しました。
これにより、従来の技術では実現が困難だった複雑なデザインをガラスファサードで表現することが可能になり、建築ファサードの設計自由度が飛躍的に高まります。
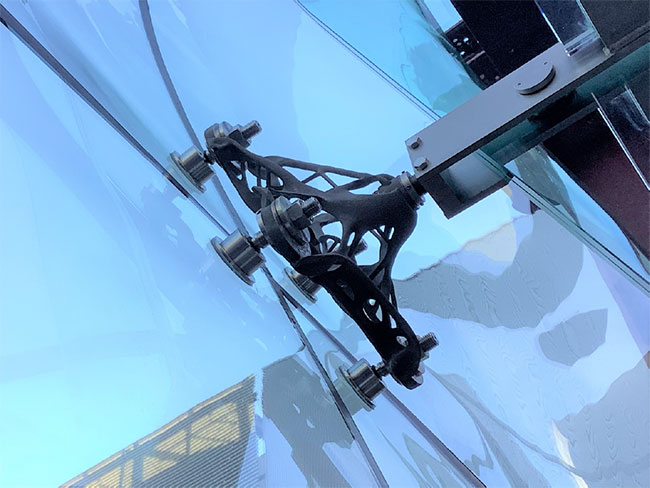
インデックス
複雑化するデザイン
近年、コンピュテーショナルデザイン手法の普及により、3次元曲面形状を取り入れたガラスファサードへのニーズが増えつつあります。しかし、ガラス部材の支持構造が複雑化する上、部材の製作精度や現場での取り付けにも高い水準が求められるため、フラットなガラスファサードと比べて施工の手間とコストが増加するという課題がありました。
低コストで3次元曲面形状を表現する手法としては、フラットなガラスをはめ込んだカーテンウォールユニットを現場で強制的にねじりながら所定の場所に取り付けるコールドベント工法が実用化されていましたが、対応できる曲率に限界があり、変化に富む複雑な曲面形状の表現は困難でした。
3次元曲面ガラススクリーン構法の概要
そこで、当社が開発したのが3次元曲面ガラススクリーン構法です。施工時に化学強化合わせガラスで成形した曲面ガラス部材と支持部材を構造接着剤で固定する構法で、支持部材の構造を最適化することにより、現場での調整を少なくでき、施工精度を確保しながら取り付けの手間を低減することができます。
支持部材の製作には、ジェネレーティブデザイン手法と金属プリンティング技術を活用しています。ジェネレーティブデザイン手法とは、ソフトウェア上に一定の情報を入力することでシミュレーションを繰り返しながら最適な製品設計を生み出すもので、接合部の構造強度を効率的に高める支持構造をつくり出し、その3次元データを粉体金属プリンタに入力して、ガラス部材の曲面形状にフィットする金属製の支持部材を一品生産します。さらに、完成した部材の形状を3次元スキャナで計測し、製作精度を確認した上で施工を行います。
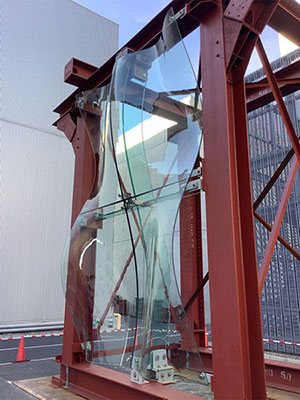
特徴
本構法では、4つの技術を組みあわせているのが特徴です。
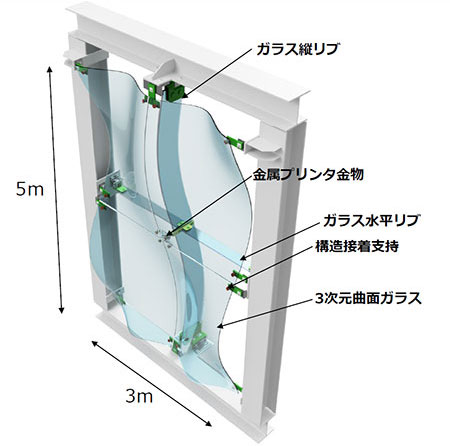
1.化学強化合わせガラスと曲面合わせ加工技術
化学強化合わせガラスとは、ガラスを薬液に浸して化学強化処理をした上で曲げ加工をする方法です。従来の手法では、熱処理をすることによってガラスを曲げていました。しかし、ガラスは熱による歪みが生じやすいため、合わせガラスにする場合の形状のずれや、現場での取り付け調整が生じやすいという課題がありました。
しかし、化学強化したガラスは、従来よりも歪みが生じにくいためデザインの自由度を確保できる上、自然現象では破損しにくいという利点もあります。
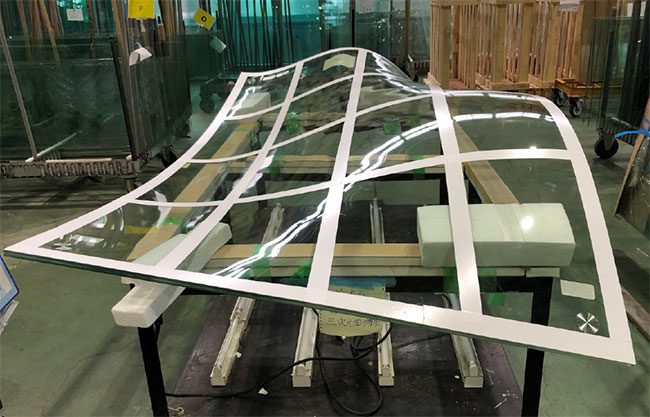
2.接着剤によるガラス接合技術
ガラスカーテンウォール構法のひとつとして、ガラス部材を点支持する構法があります。一般的な方法では、サッシ枠などの長尺の金物を用いず、ガラスの四隅に穴をあけ、そこにコネクターを通して柱などに固定します。しかし、3次元曲面ガラスでは、穴をあける場所の調整が非常に困難であり、現場での施工精度も低くなるため、本構法では穴をあけずに構造接着剤を適用して支持部材を直接接着する方法としました。これにより、従来必要とされる金物を必要最低限に抑え、シームレスで美しい自由曲面のガラススクリーンとして見せることが可能です。構造接着剤は紫外線に対しても劣化が少なく、安全に品質を確保することができます。
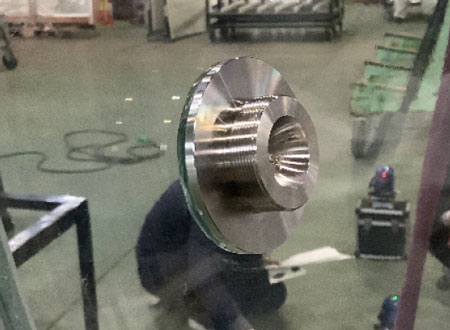
3.ジェネレーティブデザインと粉体3D金属プリンタ造形技術
複雑な形状である3次元曲面ガラス同士をつなぐクロスジョイント接合部は、ジェネレーティブデザイン手法でデザインした支持金物を粉体3D金属プリンタにより造形します。まず、風圧、地震などの数値をコンピュータに入力することで、支持金物の最適な形を検討。次に、粉体3D金属プリンタによってデザインされた通りに出力。最後に3Dスキャナによって製作精度を確認したのちに、接合部へ接着します。
ジェネレーティブデザイン手法によって、短時間で最適な形状を効率的に導き出し、3D金属プリンタによって複雑な形状の支持部材も精密に出力できるため、量産された同じ形状の支持金物を調整して取り付けるよりも施工時の手間やコストを抑え、施工後の安全性を確保することができる利点があります。
4.デジタル計測技術、精度管理技術
フラットガラスと異なり3次元曲面ガラスは耐風圧性能や層間変位などを検証することが非常に困難です。粉体3D金属プリンタで出力した支持金物の強度検証についても同様のことが言えます。そのため、検証には3Dスキャナによる形状・品質の検証、モーションキャプチャによる変位計測など、デジタル計測技術をフル活用しました。
実大実験による性能検証では、風圧や地震の揺れを与えることで性能を検証。東京都心の低層の建築であれば、問題なく適用できることが実証されました。
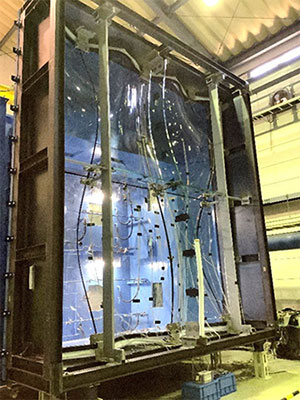
今後の展望
コンピュテーショナル・デザインの普及によって、ますます複雑なデザインが求められつつあります。それらを高精度に実現するための技術のひとつとして本構法を用いることで、デザイン価値を高めるとともに、無駄の少ない安全・安心な建築の提供に貢献していきます。